Digital Twins Revolutionize Product Development Across Industries
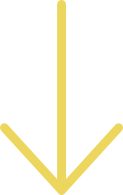
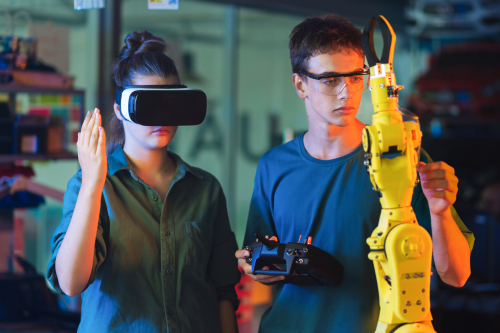
At a manufacturing facility in Stuttgart, engineers are doing something extraordinary. They aren’t just inspecting parts or prototypes on the assembly line. They’re monitoring virtual replicas that operate in tandem with the physical versions machines that move, adapt, and improve in real time. These aren’t animations or simulations. They are digital twins, and they are quietly reshaping how products are developed, deployed, and maintained.
Understanding Digital Twins: More Than a 3D Model
Digital twins are virtual representations of physical systems, updated in real time through a continuous feed of data from sensors and software. Born out of aerospace engineering and first popularized by NASA, these twins are not static models but living, evolving systems. They enable engineers and designers to run simulations, test design iterations, and monitor performance before touching the actual product.
McKinsey defines digital twins as a transformative tool that “simulate design iterations, monitor performance, and forecast maintenance needs,” all without halting production. By incorporating data analytics, machine learning, and Internet of Things (IoT) technologies, digital twins transform product development from a linear process into a dynamic, interactive cycle.
Industry Adoption: From Assembly Lines to Operating Rooms
The technology has found eager adopters in manufacturing, healthcare, automotive, and aerospace sectors. In the automotive industry, companies like Ford and Tesla use digital twins to refine engineering processes, monitor vehicle performance, and detect potential faults before they occur. With integrated sensors feeding live data into the twin, engineers can understand how a product behaves in real-world conditions and update future versions accordingly.
Siemens reports that digital twins are helping enterprises optimize factory operations, improve maintenance schedules, and develop products with unparalleled precision. These twins don’t just simulate they anticipate.
In healthcare, surgeons are beginning to use digital replicas of organs for preoperative planning. These medical twins allow for customized simulations based on patient-specific anatomy, increasing the chances of successful procedures while reducing risk. What was once speculative fiction is now becoming standard practice in elite hospitals.
Measurable Gains, Tangible Results
The return on investment is striking. According to McKinsey Operations, the implementation of digital twins can shorten time-to-market by up to 50% and reduce operational costs by 10 to 20 percent. That’s not just cost savings it’s a fundamental shift in how businesses allocate resources and manage workflows.
For manufacturers, digital twins offer more than cost efficiency. They provide clarity. Instead of relying on assumptions or historical data, companies can now base decisions on real-time insights. This means product recalls can be minimized, energy usage can be optimized, and predictive maintenance can become the norm.
In aerospace, for instance, digital twins enable engineers to detect microfractures and wear patterns in aircraft components before failure occurs. These early warnings prevent costly downtime and increase safety standards across fleets. It’s a high-tech insurance policy that pays dividends.
Not Without Its Challenges
Despite its advantages, the integration of digital twins isn’t without obstacles. One of the biggest hurdles is legacy infrastructure. Older factories and systems may lack the digital backbone needed to implement real-time feedback loops. Upgrading these systems can be expensive and time-consuming.
Moreover, the data generated by digital twins is immense. To manage it effectively, companies must invest in robust analytics platforms and skilled personnel capable of interpreting and acting on the insights. Without the right infrastructure, even the most sophisticated twin can become a digital dead end.
Cybersecurity also looms large. As more industries connect physical operations to digital replicas, the risk of cyberattacks grows. A compromised digital twin isn’t just a data breach; it could mean manipulating real-world equipment and processes with potentially dangerous consequences.
The Broader Ecosystem: Cities, Infrastructure, and Beyond
While the early momentum for digital twins came from traditional industries, newer applications are emerging rapidly. Cities are beginning to deploy digital twins of urban infrastructure to monitor traffic flow, energy consumption, and pollution levels. These urban twins allow planners to model new transportation systems or forecast the environmental impact of large-scale developments.
At scale, this kind of modeling enables governments to simulate crises from pandemics to power outages and plan more effectively. Smart cities aren’t just wired with sensors anymore; they’re reflected in fully interactive, data-driven mirrors.
The Digital Twin Consortium projects that the market for digital twins will reach $73.5 billion by the end of 2027, driven by adoption across energy, logistics, and smart infrastructure.
Digital Twins and the Future of Work
This evolution also signals a cultural shift in engineering and design teams. Collaboration now happens inside the digital twin. Instead of emailing spreadsheets or sending static mockups, multidisciplinary teams collaborate on a real-time canvas. Mechanical engineers, data scientists, and UX designers all engage with the same virtual model, creating a more agile and transparent workflow.
Plain Concepts argues that digital twins are becoming essential not just for improving design but for aligning entire teams across functions. The model becomes a source of truth a digital anchor that guides decision-making from prototype to production.
Even marketing and sales departments are getting involved. Digital twins offer a way to visualize complex products in presentations or interactive demos, improving buyer understanding and engagement. This real-time access to product behavior isn’t just useful for engineers; it’s a competitive differentiator across the value chain.
The Takeaway: A New Era in Product Intelligence
Digital twins are more than a new tool. They represent a rethinking of how we build, test, and iterate in the real world. The combination of real-time data, machine learning, and virtual simulation opens up possibilities that were unimaginable just a decade ago.
Already, leading firms are embedding digital twins into their core strategies, treating them not as experimental pilots but as critical infrastructure. They’re not asking if they need a digital twin. They’re asking how fast they can build one.
As companies and cities race toward greater efficiency and intelligence, the digital twin stands as a cornerstone of this transformation. What began in engineering labs is now reshaping boardrooms, production lines, and public policy.
And as digital twins grow smarter, they are no longer mere reflections. They are becoming the first draft of the future.
You may also be interested in: Embracing Digital: Shift from Project to Product Focus
Ready to elevate your brand and transform your vision to digital solutions? Since 2003, StudioLabs has been trusted to help conceive, create, and produce digital products for the world’s most well-known brands to cutting-edge startups. Partner with StudioLabs and create something phenomenal. Let’s chat and experience StudioLabs in action with a complimentary session tailored to your business needs!